Calebs Roofing “The Flat Roof Roofing Company”
Calebs Roofing “The Flat Roof Roofing Company” specializes in flat or low slope roofs & structures that require membrane type roofing systems. Caleb’s also manufactures and installs Metal Roofing Systems. Caleb’s well-trained and loyal roofing professionals have a reputation unsurpassed in the Denver Metro area for attention to detail and reliability. Caleb’s is a Commercial Roofing Company able to repair or replace your commercial roof today! We are “The Flat Roof Roofing Company”. Call for details.
Calebs Roofing is a Manufacturer Certified Applicator for all types of membrane roof systems. Calebs Roofing has experience with all kinds of projects from Residential Roofs to Commercial Roofs. We can handle anything from repairing a leaking roof to a complete tear off and roof replacement.
Flat roof roofing is our specialty. We know our roofs, and our professional roofing contractors are among the best in Colorado. We are Colorado’s experts at Flat Roofing for both residential and commercial roofing. For more information please call our roofing professionals at (303) 971-0256 or Click Here to request a free quote.
Below are a list of commercial roofing types to learn more about what Calebs Roofing commercial roof experts can repair, replace or install.
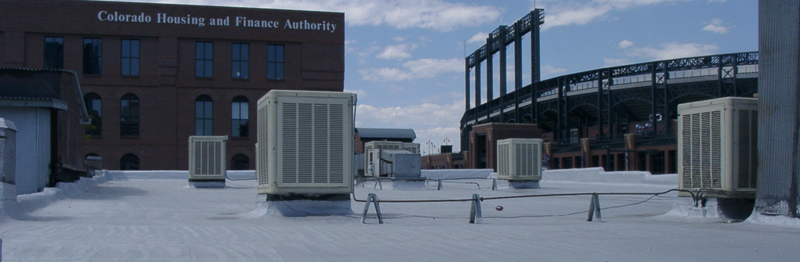
Types of Flat Roofing We Install
This roofing material can be fully adhered, mechanically fastened, or ballasted. TPO seam strengths are reported to be three to four times higher than EPDM roofing systems. This is a popular choice for “Green” building. It is available in white, grey, and black. Using white roof material helps reduce the “heat island effect” and solar heat gain in the building. However, TPO has changed formulations over the years and each manufacturer has its own mix of “polyolefins” (plastics.) This means that TPO remains largely unproven in real world applications as its current formulation exists today.
Polyvinyl Chloride (PVC) membrane roofing is also known as vinyl roofing. Vinyl is derived from two simple ingredients: fossil fuel and salt. Petroleum or natural gas is processed to make ethylene, and salt is subjected to electrolysis to separate out the natural element chlorine. Ethylene and chlorine are combined to produce ethylene dichloride (EDC), which is further processed into a gas called vinyl chloride monomer (VCM). In the next step, known as polymerization, the VCM molecule forms chains, converting the gas into a fine, white powder – vinyl resin – which becomes the basis for the final process, compounding. In compounding, vinyl resin may be blended with additives such as stabilizers for durability, plasticizers for flexibility and pigments for color.
Thermoplastic PVC roofing is extremely strong, as its heat-welded seams form a permanent, watertight bond that is stronger than the membrane itself. PVC resin is modified with plasticizers and UV stabilizers, and reinforced with fiberglass non-woven mats or polyester woven scrims, for use as a flexible roofing membrane. PVC is, however, subject to plasticizer migration. (a process by which the plasticizers migrate out of the sheet causing it to become brittle.) Thus a thicker membrane has a larger reservoir of plasticizer to maintain flexibility over its lifespan. PVC is often blended with other polymers to add to the performance capabilities of the original PVC formulation, such as KEE – Keytone Ethylene Ester. Such blends are referred to as either a CPA – Copolymer Alloy, or a TPA – Tripolymer Alloy.
Vinyl roofs are inherently fire resistant due to their chemical composition and have a broader range of fire ratings over common substrates.
PVC has been sold for commercial roofing use for more than 40 years. Vinyl roofing membranes’ long life cycle – and the associated lower energy consumption to both produce the raw material and process it into useful products – is a significant factor in their sustainability as a building product.
Vinyl roofs provide an energy-efficient roofing option due to their inherently light coloring. While the surface of a black roof can experience a temperature increase of as much as 90 degrees under the heat of the full sun, a white reflective roof typically increases only 10-25 degrees Fahrenheit.
Vinyl membranes can also be used in waterproofing applications for roofing. This is a common technique used in association with green, or planted, roofs.
It worthy of note that many Green Building organizations recommend not using PVC roofing due to significant environmental hazards from the toxicity of the manufacturing process as well as the noxious compounds released in a fire such as hydrochloric acid fumes and byproducts including dioxin, a potent carcinogen.
A bitumen is a term applied to both coal tar pitch and asphalt products. Modified Bitumens were developed in Europe in the 1970s when Europeans became concerned with the lower performance standards of roofing asphalt. Modifiers were added to replace the plasticizers that had been removed by advanced methods in the distillation process. The two most common modifiers are APP (attactic polypropylene) from Italy and SBS (styrene-butadiene-styrene)from France.
The United States started developing modified bitumen compounds in the late 1970s and early 1980s. APP was added to asphalt to enhance aging characteristics and was applied to polyester, fiberglass, or polyester and fiberglass membranes to form a sheet good, cut in manageable lengths for handling. Usually applied by heating up the underside of the roll with a torch provided a significant fire hazard and was outlawed in some municipalities when buildings caught fire and some burnt to the ground. Another problem developed when a lack of standards allowed some manufacturers to produce goods with amounts of APP insufficient to enhance the aging characteristics. SBS is used as a modifier for enhancing substandard asphalt and provides a degree of flexibility much like rubber. It also is applied to a myriad of carriers and produced as a sheet-good in rolls that can be easily handled. SEBS – (styrene ethylene butadiene styrene) is a relatively new formulation increasing flexibility of the sheet and longevity.
Ethylene Propylene Diene Monomer is a synthetic rubber most commonly used in single-ply roofing because it is readily available and relatively simple to apply. EPDM as a roofing membrane has advanced significantly over recent years. Problems previously associated with it included moisture gain under the membrane by vapour drive (occurring on roofs with air conditioned space beneath), and that EPDM did not like to adhere to itself and seam problems occurred. Simply adding a vapour barrier will help to resolve vapour drive.
Seaming has become simple with the addition of Factory Applied Tape, resulting in a faster installation. The addition of these tapes has reduced labour by as much as 75%. Rolls of EPDM are available with Factory Applied Tape pre-applied to one edge. This is an uncured EPDM tape. The other edge is marked to indicate the appropriate ovelap. The Factory Applied Tape is laid into the primed overlap and rolled with a little pressure. The resulting seam is stronger, and neater. Any details are taken care of with the appropriate tape. The process involves applying primer with a brush, allowing it to flash off to touch dry (this takes moments), then applying the tape and rolling to ensure it is properly bonded.
It is a low cost membrane, but when properly applied in appropriate places, its current warranted life-span has reached 30 years and its expected life-span has reached 50 years and this continues to rise with every year that passes.
Typically, there are three installation methods. Ballasted at 1,000 lbs/sq or 10 lbs/sq.ft. with large round stones. Mechanically attached is another method and is suitable in some applications where wind velocities are not usually high. Fully adhered is the most expensive installation method but proves to give the longest performance of the three methods.
The new generation of EPDM, with a FleeceBack, has been combined with a polyester fleece backing and fabricated with a patented hot melt adhesive technology which provides consistent bond strength between the fleece backing and the membrane. This has resulted in largely eliminating shrinkage of the product, whilst still allowing it to stretch up to 300% and move with the building through the seasons. The fleece improves puncture and tear resistance considerably and .045 mil EPDM with a fleece backing is 180% stronger than .060 mil bare EPDM. Fleecebacked EPDM has a tear strength of 39.9N/mm compared to 13.1N/mm of that without the fleece reinforcement, more than 3X the strength. Bare .045 EPDM rubber is a 1.14mm (.045) thick membrane with no fleece backing and holds a L4 puncture rating (the highest rating).