Thermoplastic Roof System aka PVC Roofing
PVC (polyvinyl chloride) and TPO () are two of the most common thermoplastic, single ply, roof system membranes. PVC Roofing is a common type of thermoplastic roof material that Caleb’s Roofing specializes in. Thermoplastic roof sheets are usually a woven polyester fabric coated with a blend of thermoplastic materials to form a flexible sheet ranging from 35 to 60 (depending on manufacturer) mils thick and is hot air or solvent welded at the seams.
When thermoplastic roof systems were first introduced in this country some manufacturers, in an effort to be competitive, eliminated the scrim which helped control shrinkage and distributed stress. Also some of the manufacturer’s formulation for their sheets were not quite right leading to product failures that gave thermoplastics a bad name. This was particularly true at high altitudes, such as the Front Range, where degradation from UV rays are more common in this material. The roofing industry has addressed these problems giving thermoplastics a significant market share.Thermoplastics tend to be high end roof systems and are more often a new construction application and are typically constructed with PVC roofing materials. Click here for technical information.
PVC and TPO roof membranes can be installed fully adhered, mechanically attached or ballasted. Most PVC roofing and TPO roofing membranes do not receive surfacing. Is a PVC Roofing System the type of roof that you need?
For more information please call our roofing professionals at (303) 971-0256 or Click Here to request a free quote.
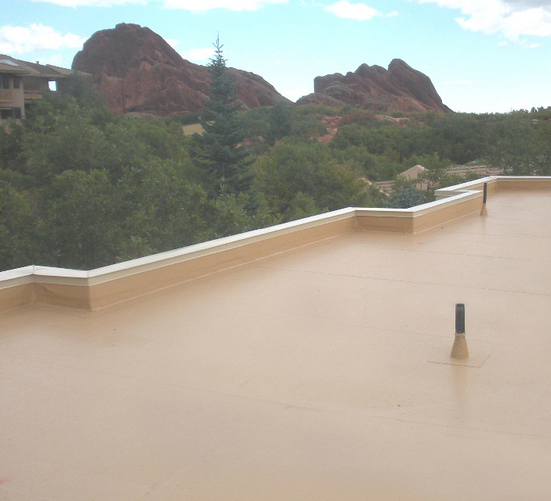